NORIS TWIN GGV HM TICN
New carbide tap NORIS TWIN GGV HM increases reliability and durability
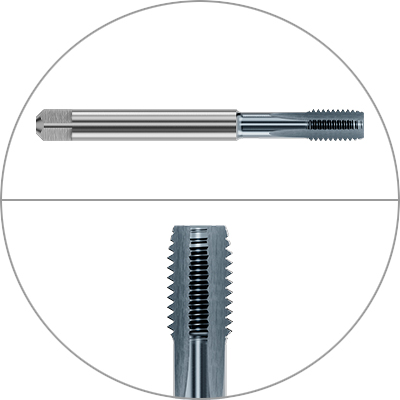
NORIS TWIN GGV HM
- Solid carbide cutting material, more flutes and optimized geometry for more tool life in abrasive cast iron materials
- Increased tolerance for more tool life in abrasive or clamping workpiece materials
- TICN coating for less wear and longer tool life
Application
- P
- M
- K
- cast iron
- 10 – 80
- Emulsion/Dry
- N
- S
- H
Available dimensions
- M
- MF
- UNC
- UNF
- G
- NPT
- M4
–
M16
ISO2X - M12x1,5
–
M20x1,5
ISO2X -
–
-
–
-
–
-
–
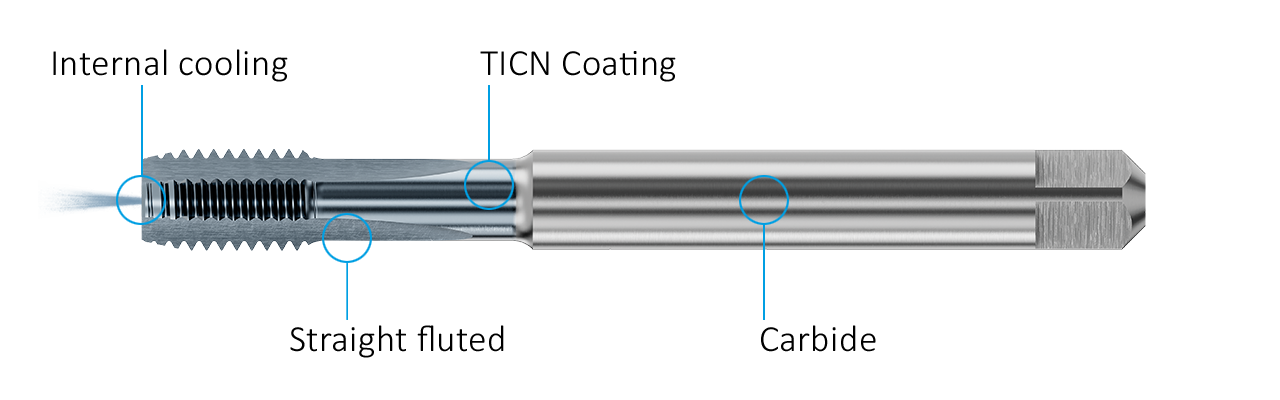
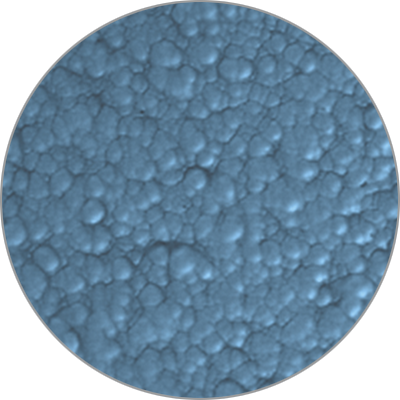
- TICN
A high hardness of more than 3000 HV and low friction values protect against abrasive wear
Coating
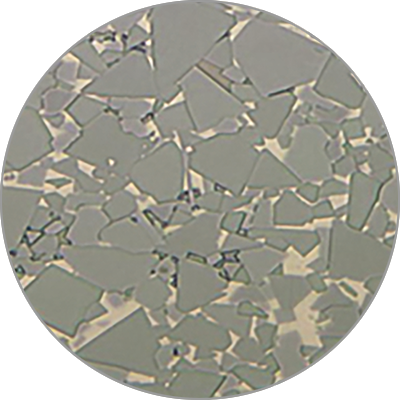
- Carbide
Tough-hard ultrafine grain grade for the processing of extremely hard materials, cast materials, composite materials, plastics and graphite - Coolant bore
Ensuring cooling lubrication and chip evacuation during machining
Substrate
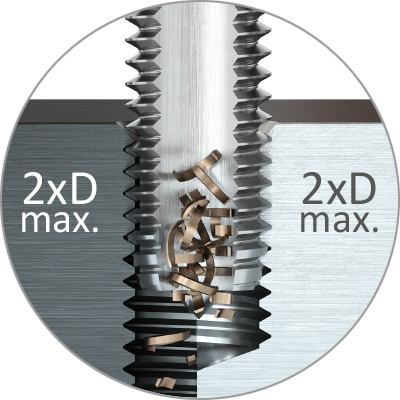
- GGV
Special geometry for modern cast iron (GJL, GJS, GJV) - Straight fluted
Stable cutting geometry achieves the greatest possible resistance to mechanical stress - Higher number of flutes
Geometry
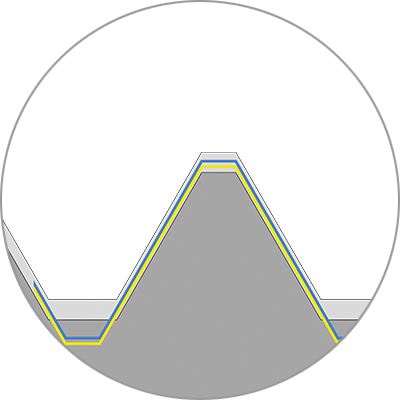
- X-Tolerance
The larger production dimension guarantees longer use, especially in abrasive and clamping materials
Thread portion
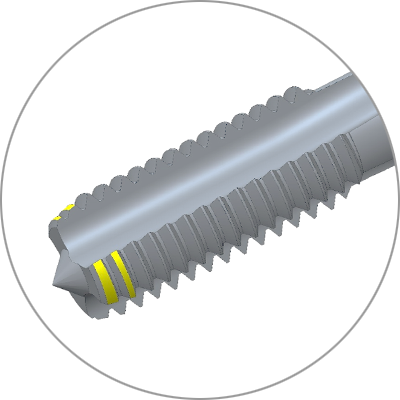
- Form E
- Short gate length for low thread runout
Chamfer length
Product-Highlights
Tool features
- Special designed geometry for cast materials
- Reduced chamfer length for short thread run out
- High quality basic material
- With internal coolant
- Higher number of flutes
Advantages
- High cutting speed
- High production stability
- Increased wear resistance
- Reduced cold welding and friction
Customer benefits
- Long machine run = higher productivity
- Increase production safety = reduce machine down time